In the world of electronics manufacturing, quality and reliability are of utmost importance. To ensure the performance of modern devices and maintain a competitive edge in the global market, manufacturers must adhere to certain standards. One of the most crucial of these is the IPC standards, which serve as a reference point for electronic assembly and manufacturing processes. So, what exactly are IPC standards and why are they so important? Let’s dive into the details.
What is IPC?
IPC stands for Institute for Printed Circuits, an international organization that develops standards for the electronics industry. IPC standards are designed to optimize the quality, reliability, and manufacturing processes of Printed Circuit Boards (PCBs), electronic assemblies, and components.
Goals of IPC Standards
IPC standards aim to improve quality at every stage of the design, production, and assembly of electronic products. Here are the main goals of IPC standards:
- Quality Assurance: Ensures electronic products perform well and have a long lifespan.
- Global Compliance: Facilitates cooperation by creating a common language between different manufacturers.
- Increased Efficiency: Optimizes production processes to reduce costs and minimize errors.
- Customer Satisfaction: Fewer errors and higher quality products build trust with customers.
Most Commonly Used IPC Standards
Here are some of the most widely used IPC standards in electronic manufacturing processes:
- IPC-A-610: Defines the acceptability criteria for electronic assemblies, particularly focusing on the visual quality requirements of the assemblies.
- IPC-2221: Contains general design rules for printed circuit boards, helping designers produce PCBs that meet international standards.
- IPC-J-STD-001: Covers the soldering requirements for electrical and electronic assemblies, serving as a reference for high-quality soldering processes.
- IPC-6012: Specifies the quality and performance standards for rigid printed circuit boards.
- IPC-7711/7721: Provides procedures for the rework, repair, and modification of electronic products.
Why Are IPC Standards Important?
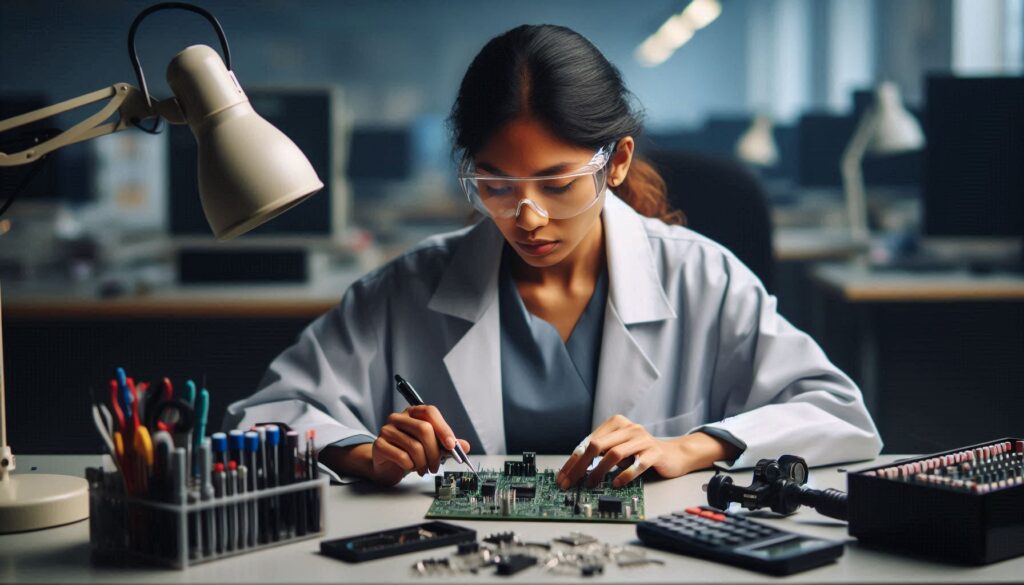
The importance of IPC standards stems from the advantages they offer in electronic manufacturing:
- High Quality: Manufacturers who comply with IPC standards gain a competitive advantage in the global market by ensuring high-quality products.
- Reduced Error Rates: Minimizes errors in production processes, leading to increased efficiency.
- Customer Trust: Products adhering to IPC standards build trust with customers and enhance the brand’s reputation.
- International Acceptance: Products that meet IPC standards are globally recognized and facilitate smoother supply chain operations.
IPC standards are critical to ensuring quality and reliability in the electronics industry. Serving as a guide for designers, manufacturers, and engineers, these standards also contribute to the advancement of the industry. By adopting IPC standards in your electronics manufacturing processes, you can gain cost advantages and enhance your competitiveness in the global market.
Tip for You: If you are working in electronics design or manufacturing, mastering IPC standards will provide you with a significant advantage. To learn more about these standards, you can visit IPC’s official website.
React with emojis!